Carbon Fibre Part 1
Raoul Luescher takes an in-depth look at carbon fibre, how it is made and its strengths and weaknesses.
Not that long ago, carbon fibre was considered a fragile material only suited to weight obsessed cross country racers. These days, carbon fibre is popping up everywhere—from long travel trail bikes to downhill rigs. Some still feel that the use of carbon is a fad and believe that it should remain on the road while others see it as the future. In either case, there is no denying that it is a major part of the modern day MTB market. So what is it, how is it used on mountain bikes and what are its limitations?
Carbon composites as we know them are a blend of carbon fibres with a polymer matrix. The fibre provides very the high tensile strength and most importantly stiffness, the polymer matrix holds the fibres rigid so each fibre can transfer load to the next fibre. With composite materials an engineer can design specific mechanical properties to handle a particular problem. Want a bike that is torsionally stiff for good power transfer but vertically compliant for comfort? Carbon composite can do it, and do it at a very low weight.
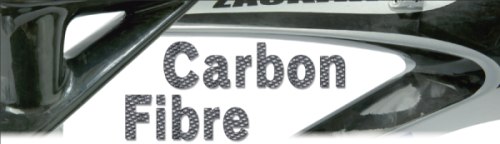
About the Fibre
There are many different types of carbon fibre as well as other fibres such as aramid, ceramics and of course glass fibres. Basically, and without too much engineering jargon, the most common grades of carbon used in cycling are known as T300, AS4 and T700. Some companies are also using ‘high modulus’ fibres of various grades such as T800, MJ 50 and others. What is Modulus? Modulus refers to the stiffness value of a material—it has nothing to do with strength. This is important because the two terms are often used incorrectly; stiffness is the rate of deflection, strength is the load that can be resisted. High modulus fibres have a higher stiffness than standard modulus fibre, in fact they can be more than twice as stiff. Bike frames generally are limited by stiffness, so using high modulus fibre means that less material is needed to meet the design requirements, thus a lighter bike is the result
However high modulus fibre has less elongation and lower strength, so using less of it makes the frame or component less damage tolerant than standard modulus. High modulus fibre is also very expensive; these factors can limit its use in mountain biking. Sometimes blends of different fibres are used at various locations on a frame. This starts to get complex so the designer really has to know what is going on with each layer and how it interacts with other plies within the frame for this to be successful.
Fabric Types
There is a lot of talk about ‘unidirectional’ and ‘multidirectional’ fibre, so here is a very basic explanation. Wherever you see the carbon ‘weave’ you are looking at a multidirectional fabric. This is made by weaving bundles of carbon filaments called ‘tows’. These tows are commonly made up of 3,000, 6,000 or 12,000 individual carbon fibres—these are referred to as 3k, 6k 12k etc. There are many different styles of weave that give different properties and looks. Unidirectional has the fibres running in one direction only and doesn’t have the same woven look. Some advantages of woven fabrics are that it is easier to place in complex shapes, it is more damage resistant and it also looks good. Disadvantages include slightly lower mechanical properties, it is more expensive and it is slightly heavier. Often a woven outer layer is used with unidirectional material underneath. This blends the better protection and look of a woven fabric with the lighter weight, greater strength and lower price of unidirectional carbon.
Fibre Direction
Why do people talk about the direction of the fibre, what does this mean? Individual filaments are only strong along their length. This means a unidirectional material is only strong in one direction, woven bi-directional material is strong in two directions.
This is where the design engineering comes into it. By placing layers at different angles, an engineer can dial in the properties required. This is the reason that carbon frames can be stiff when you stand on the pedals and comfortable at the same time. This is the major difference between composites and metals. Metals have the same strength and stiffness in all directions, the only things metal tube makers can change is wall thickness and the diameter/shape of the tube. So the direction that fibre is placed in a structure is very important to the final outcome and must be controlled during manufacture. Unidirectional material gives the designer very good control over what each layer of fibre is doing and they can optimise the part if they know how the loads are applied. We will talk more about this a bit later.
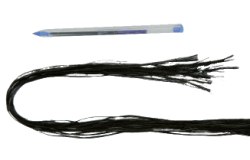
About the Resin
It can get just as confusing with the resin or ‘matrix’ as it is known. The matrix resin is used to encapsulate the fibres and bond each fibre to the others around it. This allows each fibre to transfer load to the next and thus create a rigid product. Remember it is the fibre that has the high tensile strength and stiffness; the resin is weak compared to the fibre.
What are the resin choices?
In most cases, epoxy resins are used for bike parts—it is similar to the ‘Araldite’ glue that you may use around the house. As with all the different types of fibres there is a broad choice of epoxy resins. Some resins are ‘toughened’ which means they have additives to limit crack growth. Resin selection is dependant on the environment that you want it to perform in; compared to aircraft, mountain bikes have got it pretty easy with far less variation in temperature and other environmental factors.
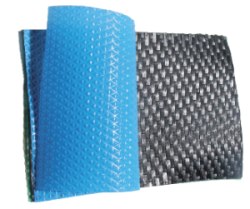
What is ‘Prepreg?’
These carbon fibres come supplied with resin pre-impregnated. This fabric with resin has to be stored in a freezer until ready to use. It is cured at an elevated temperature usually from 80 C to around 180 C and does not require resin mixing prior to use. The advantages are many, especially with handling and quality.
What is Carbon Nano Technology?
Some marketing material talks about Carbon Nano Tubes—this also refers to the resin blend. Carbon nano tubes are currently the strongest and stiffest material known to man. They are very small carbon tubes about 1/50,000th the diameter of a hair that can be added to the resin to reinforce it and hence improve its properties—like adding gravel to cement to make it tougher. Some of the data on this looks good in terms of improving toughness and strength. Carbon nano tubes are very expensive, however only small amounts are required.
Manufacturing Techniques
An assortment of techniques can be used to form the fibre and resin into the desired shape. These methods may be used to create frame components (tubes & lugs), complete frames or other bike parts such as cranks or handlebars
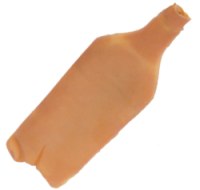
Bladder Moulding
Bladder moulding is very common on cycling products. One piece or ‘monocoque’ frames are made this way, as are most of the lugs and tubes used in a bonded frame. Most hollow tubular parts are bladder moulded as well as rims, handlebars, even some cranks. Bladder moulding is where the fibre is pressed against a mould by a plastic or rubber bag inflated to high pressure inside the hollow carbon section. Prepreg material is generally used due to its ease of handling.
Tape Laying
Tape laying is a computer controlled method for making tubes. Layers of fibre tape are continuously wrapped around a mandrel by a robot and then cured. This method is not that common in cycling, however it is one of the best ways to make a round tube. Some tubes used in tube and lug type frames are made in this manner. Compression Moulding Used extensively in the automotive industry. This method involves placing fibre, usually a random orientation prepreg mat, into a closed mould then simultaneously heating and pressing it. It is used for small parts such as suspension pivots, cranks, where loads are not defined. So as you can see there are lots of choices for composite engineers to select the fibres, resin and the process from.
Frame Construction
Much of the jargon refers to the frame construction techniques. There are a few different ways to make a bike frame. It can be made in one piece, often termed monocoque, or it can be made in smaller pieces that are assembled to form a whole. Other common methods include using tubes and lugs that are secondary bonded in a jig, or the tube to tube method which is also made in a jig. Although one piece frames can have a performance advantage when made properly, history has shown that quality control problems can be encountered in a production line environment. Setup costs are also restrictive due to the number of costly moulds required to get a good range of frame sizes.
Therefore, most modern carbon bikes are secondary bonded. The parts are made and cured separately, and then the individual parts are assembled with adhesive to create the full frame. This has many advantages in a production line environment. It is much easier to control the manufacturing process of a single tube or component than a complete bike. This provides a higher level of quality control when compared with one piece frames. If a problem is found in one section, it can be discarded and a new one made, so only a relatively inexpensive part of the frame gets scrapped. A problem in a monocoque may result in the whole frame being scrapped, which can be expensive. This leads to quality advantages with the secondary bonded method. The disadvantage of a bike made this way is that assembly needs to be done carefully and bonding can have its own problems. It also requires more finishing work which is labour intensive. The ‘tube to tube’ method, sometimes referred to as ‘carbon welding’, is similar in that the frame is also made from a collection of smaller pre-cured parts. The tubes are placed in a jig and bonded, then more carbon is wrapped around the joint to provide strength. This method requires careful finishing around the joints to ensure the integrity is not compromised. It is a very labour intensive process that is commonly used in Asia, or for very low volume custom work. It is possible to make very good frames with this method.