Carbon Fibre Part 2
Other methods combine the lugs and the wrapping methods, where tubes and lugs are bonded and then a layer of carbon is placed over the joint to reinforce it and create a seamless look. This overcomes some of the potential bonding problems, but also requires more finishing work.
The Big Picture
So what makes a good composite bike you ask? There are many factors that all must be met to produce a good carbon bike. Firstly the design must be created by people who are experienced with using composite materials. By this I mean engineers who know how these materials behave under load. Composites got a bad reputation in the seventies because people basically replaced aluminium or steel with carbon composite without understanding its behaviour. A well designed frame will be stiff, strong, light and have a long fatigue life.
Secondly, selecting the most appropriate manufacturing method for the design is paramount. There are many different ways to make composite structures, each method suited to certain types of components. This must be considered during the design stage.
Thirdly, the materials used must be appropriate for the task. This means selecting the right fibre type and form; i.e. woven, braid or unidirectional. The right resin system for the manufacturing process is also important along with its environmental properties.
Does it get soft in the boot of your car on a hot day? Last but by no means least is the quality control aspect of the process. Does each frame meet the intended quality standards so it delivers the performance that the designer intended? This is very important with composites; the aerospace industry spends a lot of money inspecting products to ensure that they deliver a consistent standard of performance. With metals you know the properties of the tubing before it is welded because it is certified by the tube manufacturer. This is generally not the case with composites; the builder has to have their own quality control facility to ensure that a safe product goes out the door.
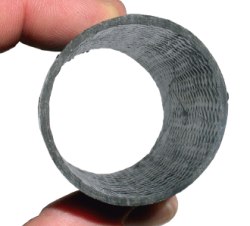
Structurally the conventional double diamond shaped frame is very efficient; it had to be because the materials used in the early days weren’t nearly as good as today’s offerings. A well designed straight round tube is still very hard to beat and most fancy tube shapes are based around marketing. However, it does get interesting with modern dual suspension rigs as you need to fit pivots and a shock into the frame design— composites can offer great flexibility in this regard. Other ideas such as using designed in flex to create a pivotless suspension system are entirely possible, utilising the properties available with composites—check the Cannondale Scalpel reviewed in this issue.
What about the ride?
Why is it that some carbon frames are very stiff and a bit unforgiving when others can ride really smooth yet still deliver the power to the trail? The answer lies within the points that I have already covered. It is possible to dramatically change the ride by changing the grade of carbon, the number of layers (called plies) and the orientation of the plies. It comes down to the level of design engineering and selection of materials. Getting the balance just right for a particular riding style can be tricky, to make it so its suits everyone is just about impossible. Back in the days of custom metal frames, the frame builder would select particular tubes based on your weight, height and riding style. With production metal bikes this ceased to happen. Now the majority of carbon bikes are made on mass in a controlled production facility to keep close tabs on the quality level and reduce the manufacturing cost. So, even though composites can be customised to a very high level, they seldom are because it is just too expensive. Bike companies tend to target a particular set of ride qualities and engineer the frame accordingly.
What about carbon for recreational use?
Trail riders are now able to enjoy some of the performance advantages previously only available to XC racers. Everyone likes riding a lighter bike, as long as it can handle the type of riding asked of it. Some of the new long travel carbon fibre dual suspension bikes are half a kilo lighter than their metal predecessors. A lighter bike makes riding more enjoyable and that is what it’s all about for most people. Reputable manufacturers rely on engineers who test their bike designs on machines that simulate years of hard use within a short time and use this information to refine their designs. The production line is also refined to ensure consistent quality control and minimise any warranty issues. A carbon fibre trail bike made using this design process will provide years of trouble free riding. Composite materials are also great for components such as bars and seat posts as these are relatively easy parts to make at consistently high quality level. Other parts such as wheels are coming into the market with the two opposite ends of the spectrum being covered. Very light rims for XC racing are becoming available and at the other end there is the virtually bombproof TAG full composite wheel designed for aggressive downhill riding.
What should I look for in a carbon bike?
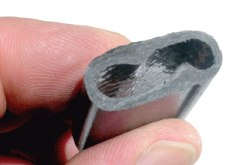
Things to look for include:
• Does the frame have a good reputation for quality?
• Does the fibre look evenly placed with no wrinkles or distorted weave?
• Are the corners well rounded to help distribute stress?
Look inside the tubes where possible.
• Does the thickness look even? Are there wrinkles? Is there extra adhesive?
• Does the exterior have lots of filler covering up problems?
Quality, quality, quality!
Quality control in composite manufacture is difficult and expensive. In aerospace it often takes longer to perform the quality checks than to make the part. Every step of the process is controlled to achieve consistent results. At the end of the line, ultrasonic scans and X-ray images are commonly used to check for compliance. These extra steps would make carbon bikes way too expensive, so manufacturers rely on process control combined with designing in a factor of safety. This means they control the steps of manufacture as closely as possible and they design quality into the part, which minimizes the things that can go wrong. Having a large ‘safety margin’ in a design gives you some leeway; if things aren’t perfect the part will still meet the minimum strength requirements. Have you noticed how the weight of carbon frames is coming down each year? This is because the size of the safety margin decreases as the manufacturing process and quality control gets better—there is a limit however.
What happens when I crash?
Firstly, let me say that a well engineered composite part can take an enormous amount of punishment and survive; you just have to look at Formula 1 cars to see that. The main pod that the driver sits in is designed to hold together whilst the rest of the car breaks up to absorb energy. It is possible to break a carbon frame just as it is possible to break anything if the design loads are exceeded. The difference with carbon is that it does not bend, it either can take the load or it cannot. This can sound scary, however in reality the strength is very high and there is usually some warning in the way of delamination and cracking due to the interaction of different ply angles. It really does come down to the design; if it is designed and manufactured well, it is no more likely to fail catastrophically than a metal part.
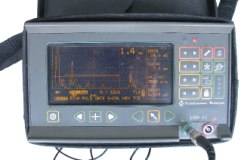
It is good practice to regularly check your bike for damage and cracks regardless of what it is made of. Cracks in the paint on lugged bikes around the join can be quite common—this is caused by the paint flexing at the joint. Although usually not a problem it is best to get it looked at. Pronounced gouging caused by dropping the chain or excessive chain suck is far more serious. This may cause breakage in the fibre or even delamination which can significantly weaken the frame. This is a limitation with carbon; it doesn’t handle scrapes very well. This type of damage is best avoided by having guards to protect the carbon in these areas. A frame that is engineered with mountain bike use in mind should have extra plies of carbon or Kevlar in vulnerable locations such as the drive side chain stay and the rock damage prone down tube. The most common problem is usually impact damage caused by dropping the bike against a hard object.
This can cause local delamination at the impact site—similar to a dent on a metal tube. All these types of damage need to be assessed by an expert to really know if the structural integrity of the frame has been compromised. There are numerous methods for evaluating the extent of the damage but it requires a lot of experience to assess the damage accurately. So if you do find something that you are not sure about, take it to your shop and ask them to get it looked at by someone with experience. For something like a handlebar it is best to just replace it.
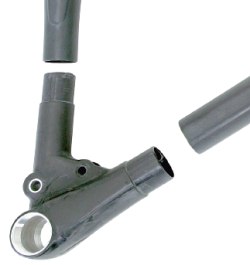
Each damaged carbon part needs to be evaluated on a case by case basis, the same as with any other material. Carbon repair methods are well established in the aerospace industry and have proved to be very effective. In many cases a carbon repair on a metal frame may be preferable as it avoids any heat damage. With good knowledge of these methods, it is even possible to do field repairs with very little special equipment and no mains power. I have repaired many frames that have suffered damage – usually caused by exuberant baggage handlers – the night before a major race with no issues whatsoever. However you need to get a specialist to look at the damage, I have seen people try to fix holes in their frame with a home fibreglass repair kit; this is definitely not recommended. Take it to someone who knows what they are doing. Mountain bikes usually see plenty of knocks and bumps that will mar the outer finish of the carbon. Where the marks are in the top coat with no damage to the underlying fibre, the surface can be resealed with some clear lacquer. Resealing the carbon will protect the fibres from further damage from oil, aggressive degreasers, UV light and moisture related damage.
A Carbon Fibre Future
Composite materials have made major inroads into the mountain bike market and carbon fibre usage is increasing across all areas of off-road use including BMX. All of this suggests that the off-road market will follow the road market and embrace the performance advantages of composites. It seems that every day some new carbon fibre part is let loose on the market. Some products are clever in their application of composites, other’s it seems are carbon for the trendy look without an engineering advantage. Be warned that composites do have limitations—aerospace engineers do not set out to design an entire aircraft from carbon, they use the best available material for the job, be it steel, aluminium, titanium, composites or whatever. Reliable performance is far more important than fashion. Look for products from reputable manufacturers, preferably with a solid history using composites, companies with a quality test program. Think about this next time you find yourself drooling over some funky looking carbon fibre bike part.