Dirt and Carbon
How fragile is carbon and what should you do if damage occurs? Raoul Luescher offers his advice.
There have been lots of questions lately regarding the durability of carbon fibre mountain bike frames and components. Some people suggest that carbon composite is not suitable for off road use, saying that it lacks durability. Is this true? Do carbon composite frames and parts have a future in our sport? Many criticisms are based on comparisons that don’t take into account some common performance characteristics such as weight, ride quality and so on. Is it realistic to expect a 1.0kg carbon frame to be as rugged as a 1.8kg steel frame? How durable would a 1.0kg metal frame be? How durable is a 1.8kg composite frame? In the end would you rather ride a 9kg bike or a 14kg bike?
Advanced composites have a proven record in high stress applications such as aerospace, defence, motor racing and a range of other sports. Carbon parts were trialled in the 1960s on commercial aircraft and are now used extensively. The material has proven itself in this market; it is not new and the next generation of commercial jets use composites for the majority of the primary structure. Nobody likes planes falling out of the sky, so if carbon wasn’t suitable it would not be used. In aerospace, materials and processes that are unreliable are avoided, for example there aren’t many welded aluminium primary structures due to the inconsistencies with welding. Anyone out there remember all the welded aluminium stem failures in the past?
Why do we have this perception of fragility with carbon parts?
There are many reasons; firstly, carbon parts are often built to be very light. Parts that push the limits are more likely to fail regardless of the material used. Carbon is a relatively new material in the cycling market and early generation products were often poorly made or designed. Engineering design and the manufacturing process both play a huge role—as designers better understand the way a material responds under load, they can design better parts.
Quality control in manufacture is also very important. The volume of parts in today cycling market means that all this engineering is now cost effective where previously it was prohibitively expensive.
Carbon Repairs
So what do you do if you suspect some damage and is it possible to repair a carbon frame or part? Most people say ‘no’ because they are not familiar with the repair methods commonly used with advanced composites. However, with the correct equipment and knowledge, it is quite straightforward to perform a composite repair—in some cases composite repairs are performed on metal structures where traditional repair methods are not practical. As a passenger on a commercial airline it is likely that you have flown in a repaired aircraft, these processes are more common than you think. They do however require some specialist knowledge to ensure the part is still suitable to use.
Over the years I have seen many poor attempts on bike repairs, the most common problems are poor surface preparation, incorrect adhesive or resin selection and a lack of understanding about the loads on the structure. I have seen home repairs using five minute Araldite, automotive putty, even home fibreglass kits. None of these are suitable for structural repairs as special adhesive resins and materials are required.
What types of damage are typical in mountain biking?
The most common is impact damage from crashes, followed by scrapes and gouges. If an impact has sufficient energy it can cause delamination and cracking. Delamination is where the individual plies in the laminate are separated so they can no longer transfer load to each other. All this happens below the surface so is often difficult to detect visually. Cracks are usually more obvious and regular inspection when cleaning your bike will help in early detection. Scrapes and gouges are also common from crashes and chain suck. Sometimes this can cause a delamination but in most cases a ply or two near the surface is damaged.
So how do you know the extent of the damage?
An ultrasonic scan is the best method to check for delamination. Ultrasound waves are directed into the part and the response is monitored to detect any irregularities. Special equipment is required as well as specific knowledge on the nature of the part. Some geometric shapes are also difficult to scan. X-ray is another method often suggested, however it is very expensive and also limited in the type of indications it can find. It is usually more appropriate during the manufacture of a bike than for picking up on typical crash damage. A thorough visual inspection in conjunction with a ‘tap test’ is another method whereby a skilled technician with a tap hammer or even a coin can get a reasonable indication of the extent of the damage.
What’s involved in a carbon repair?
The basic steps are as follows:
- Once the full extent of the damage has been assessed, a decision can be made on whether a repair is practical or not. It may be more appropriate to replace some parts such as handlebars, seat posts or saddle rails, as the repair cost often outweighs the replacement value.
- The damaged area is removed by cutting or grinding out that section. Care is taken to ensure further damage is not done to the part.
- The replacement laminate is then designed to meet the structural requirements. It is critical to match both the strength and stiffness of the existing part. By matching the original fibre type and ply angle, the repaired part will perform in a similar manner to before. Using specific materials that are optimised for repair techniques improves the performance of the repair.
- The existing material’s surface is prepared for bonding to the new material. It is critical that the surface is prepared correctly if the new material is to bond properly to the existing material. Any shortcuts here or contamination will lead to a failure of the repair.
-
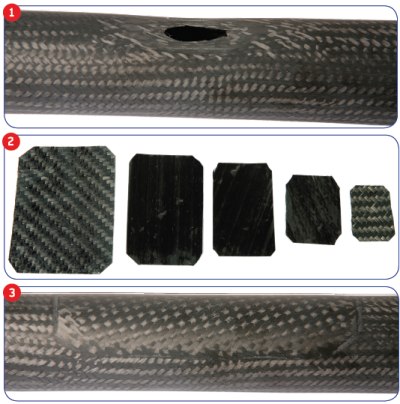
- The new material is placed, taking particular care to match the fibre orientation to provide optimum load transfer. Typically, each new layer of material is pre-cut to the exact size and angle required.
- The repair patch is then compacted using pressure or vacuum and cured at an elevated
-
Depending on the location and size, different methods are used to apply pressure and consolidate the new material. An elevated cure temperature provides higher structural properties and greater stability.
The repair is then inspected, preferably using a method such as ultrasound to provide data on the repair quality. It is important to verify that the repair material is sound so the repair behaves as per its design.
- Finally, the finishing work is done to blend in the repair and match the paintwork. It is not only good practice to finish off a repair so it looks good; this step also helps to protect the material from environmental exposure, which can reduce the performance of a repair.
Rational Perspective
So, before you buy into the argument that carbon has no place on the dirt, educate yourself on the facts and make fair comparisons between bikes and parts of differing materials. In many cases the anticarbon prejudice is based on parts that are eitherpoorly designed or at the cutting edge ofthe weight race. However, we are now seeingcarbon frames and other parts that arerobust and designed to withstand the rough and tumble of every day off-road use.While modern carbon parts can bestronger and more rugged than their alloy counterparts, damage is still possible.
With that in mind, here are the main points to consider:
- Regular inspection and cleaning can save you from catastrophic failures and crashes.
- If in doubt about any damage, get it inspected by an experienced technician.
- It is cheap insurance to replace critical parts such as bars, stems and seat posts if you find damage or after a long period of heavy use.
- Some types of damage can be repaired at a reasonable cost—you may be able to get that expensive frame back on the trail.